CRCP in Texas – Enhancing Infrastructure, Sustainability, and Minimizing Maintenance Costs
The following is a special contribution from Nancy Beltran, PhD., Director of Concrete Pavements, Cement Council of Texas; Elizabeth Lukefahr, P.E., Executive Director, Texas Concrete Pavement Association (TCPA); and James Mack, P.E., Director of Market Development – Infrastructure and Sustainability, Cemex. They explore continuously reinforced concrete pavements (CRCP) and why it is highly regarded for its resilience and dependability.
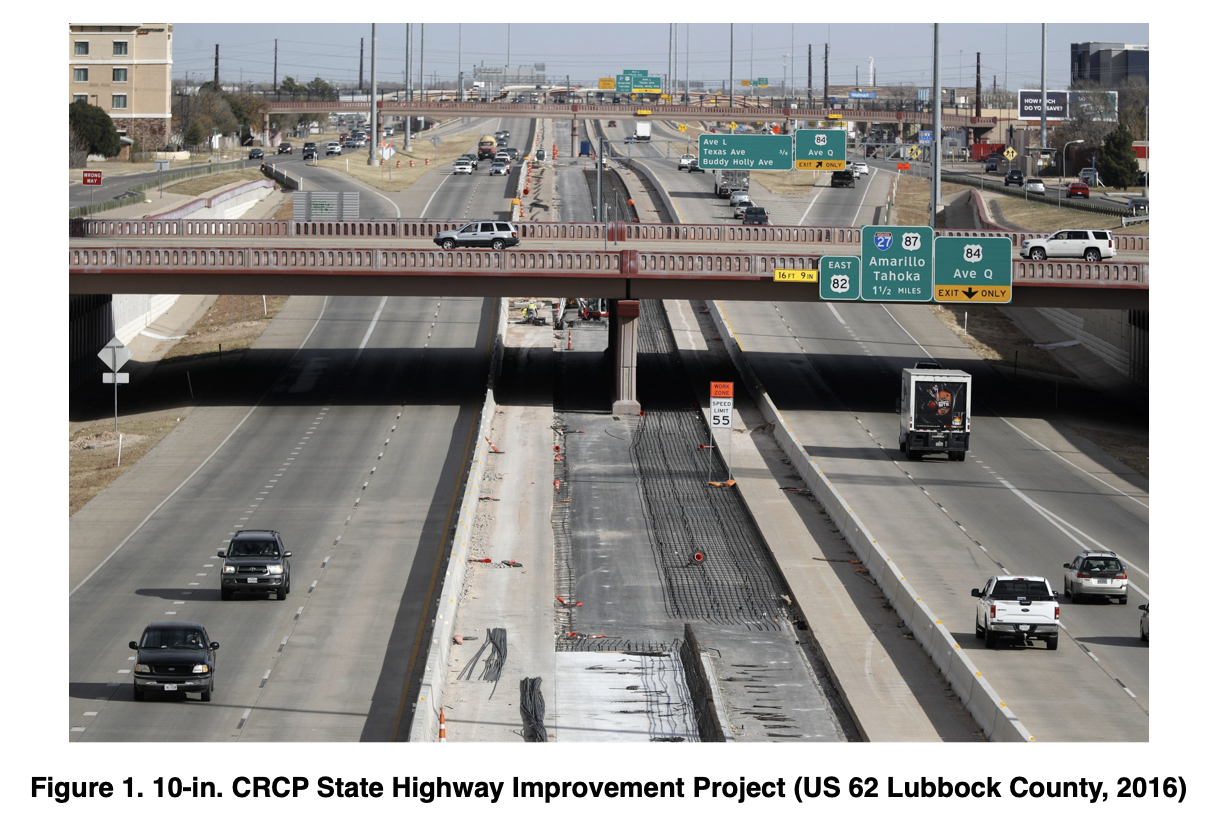
When it comes to building highway pavements in Texas, concrete is always the first choice due to its long-lasting and low maintenance advantages, and continuously reinforced concrete pavements are predominant due to their ability to handle heavy traffic and extreme weather conditions.
Design Principles
CRCP is characterized by the presence of continuous longitudinal steel reinforcement throughout the entire pavement section. The reinforcing steel bars serve a vital role by providing tensile strength to control the occurrence and propagation of cracks. The arrangement of this reinforcement system is purposefully designed to uphold the structural integrity of the pavement against a range of factors, including shrinkage, temperature fluctuations, and the stresses induced by traffic loading. Unlike asphalt pavements, CRCPs are engineered to offer 30 years of service life, with most surpassing their design life requiring little to no need for repairs. This sharply differs with the maintenance schedules of other pavement types; for instance, asphalt pavements typically require repairs every 10 to 15 years, jointed plain concrete pavements (JPCP) have a lifespan of 25 to 35 years before rehabilitation, while CRCPs stand out with their durability, requiring rehabilitation only after 43 years or more of service.
As per the Texas Department of Transportation (TxDOT) policy, the minimum thickness for CRCP is 7 inches, while the maximum thickness is 13 inches, with ½-inch increments, and all reinforcing steel and tie bars should consist of Grade 60 deformed bars. The longitudinal steel bars are placed at mid-depth of the concrete slab for CRCPs under 10.5 inches in thickness, or at 5 inches from the surface for CRCPs whose concrete layer thickness is between 10.5 inches and 13 inches. For CRCP thicker than 13 inches, two-layer reinforcement is required, whereas for 13-inch CRCP, it is optional. This placement ensures effective steel placement to resist tensile stresses induced by environmental loading.
The thickness of the concrete layer is determined based on factors such as traffic loading, base type, subgrade stiffness, and environmental conditions. TxDOT’s current design procedure for CRCP makes use of a mechanistic-empirical design procedure to determine slab thickness based on design life, traffic loading, subgrade treatment and base layer criteria. The reinforced concrete layer is usually placed over a 4-in. hot-mix asphalt (HMA) base, or a 6-in. cement treated base (CTB) with a 1-1.5-in HMA layer (bond breaker). We advise opting for the 6-inch CTB to ensure sufficient structural support. One or more subbase layers may also be used, and the last layer consists of treated or untreated subgrade. Subgrade treatment is selected based on the plasticity index (PI) of the in-situ soil. For soils with a PI of less than 35, cement alone is a great option to provide adequate strength to the subgrade layer. For soils with a PI of 35 or greater, it is recommended to treat with a combination of lime and cement. To determine the best soil and base treatment, the reader is encouraged to review the Treatment Guidelines for Soils and Base in Pavement Structures Guide.
For more information about TxDOT’s rigid pavement design procedure, visit TxDOT’s Pavement Manual, Chapter 8.
Construction Methods
Like all products, the quality of construction is essential to obtaining a CRCP that will exceed expectations, even under traffic levels far greater than the assumptions used for design. A skilled contractor will know how to provide a stable working platform and subbase and base layers that meet stiffness and non-erodibility requirements to perform for the entire pavement life cycle. Accurate grade control is essential, both to avoid waste/excess material use, but more importantly, to ensure the overall concrete thickness and location of the reinforcing steel are within specified tolerances. Proper crack control requires the steel mat to be located as described in the preceding section. An overly thick pavement with steel reinforcement lower than specified will have the potential for poorer crack control, which could result in spalling and partial-depth distress over time.
While CRCP is more easily constructed in long, unobstructed stretches like controlled access highways, there are thousands of miles of CRCP placed in urban environments. The presence of manhole covers, drainage inlets, and especially the need to keep driveways accessible are some of the more challenging construction aspects in an urban environment, especially when trying to achieve a high level of pavement smoothness. Perhaps the greatest challenge in constricted spaces is the need to deliver the concrete to the slip-form paver, as this generally requires a lane-width in addition to the paving width. However, an experienced contractor can often find solutions to staging and access challenges, so providing the freedom to innovate can improve the likelihood for a successful final pavement.
Jointing techniques are mostly similar in CRCP as to JPCP, including the need for proper timing and depth of saw cuts for longitudinal joints. A major difference between the two pavement types is the absence of regular transverse contraction joints. Since most in-service CRCP distresses occur at transverse construction joints and repair joints, the construction and inspection at the beginning and end of each day’s paving should be a primary focus for new projects. This emphasizes the importance of good construction practices during evening headers and morning concrete pouring, particularly in terms of proper compaction and curing. Similarly, terminal expansion joints require extra skill and attention in both design and construction. For more comprehensive information, Chapter 9 of TxDOT’s Pavement Manual (txdot.gov) provides valuable background details, and it is strongly encouraged that readers review the manual in its entirety.
Durability and Cost Benefits
CRCP offers several durability and cost benefits compared to other pavement types, which makes this pavement type a preferred choice for infrastructure projects requiring long-term performance. Since 1985, CRCP in Texas are designed to deliver service lives of 30 years; however, these pavements have consistently surpassed this expectation. TxDOT’s Maintenance Division conducted a CRCP service life analysis based on projects within Texas utilizing the 1996 Pavement Management Information System (PMIS). The findings revealed that as of 2023, CRCPs in Texas have averaged approximately 39.5 years of service before requiring rehabilitation, such as overlay-type rehabilitation and long stretch replacement, with many still maintaining their structural integrity in a conservative state.
With fewer repairs and interventions needed, the ongoing maintenance costs are substantially reduced compared to other pavement types. Similarly, the extended lifespan of CRCP also translates to long-term cost savings by minimizing the need for expensive reconstruction or rehabilitation projects. While CRCP may involve higher initial costs compared to traditional pavement alternatives, the low maintenance requirements of CRCP translate to cost savings over the pavement’s service life. By conducting life-cycle cost analyses (LCCA), transportation agencies and project stakeholders can assess the total cost of ownership over the pavement’s entire lifespan. LCCA considers not only construction costs but also maintenance, rehabilitation, and future replacement expenses. In many cases, CRCP has demonstrated lower life-cycle costs compared to alternative pavement designs, thanks to its superior durability and reduced need for ongoing maintenance and repairs.
In 2013, TxDOT’s Construction Division and the Wichita Falls District conducted a life-cycle cost analysis of CRCP (rigid) versus HMA (flexible) pavements on US 287/US 81 in Montague County. The results indicated that while the initial construction cost for CRCP was higher, its long-term maintenance costs were significantly lowered compared to HMA (refer to Figure 2). The cost per square yard for this study concluded at $42.65 for CRCP and $45.57 for HMA.
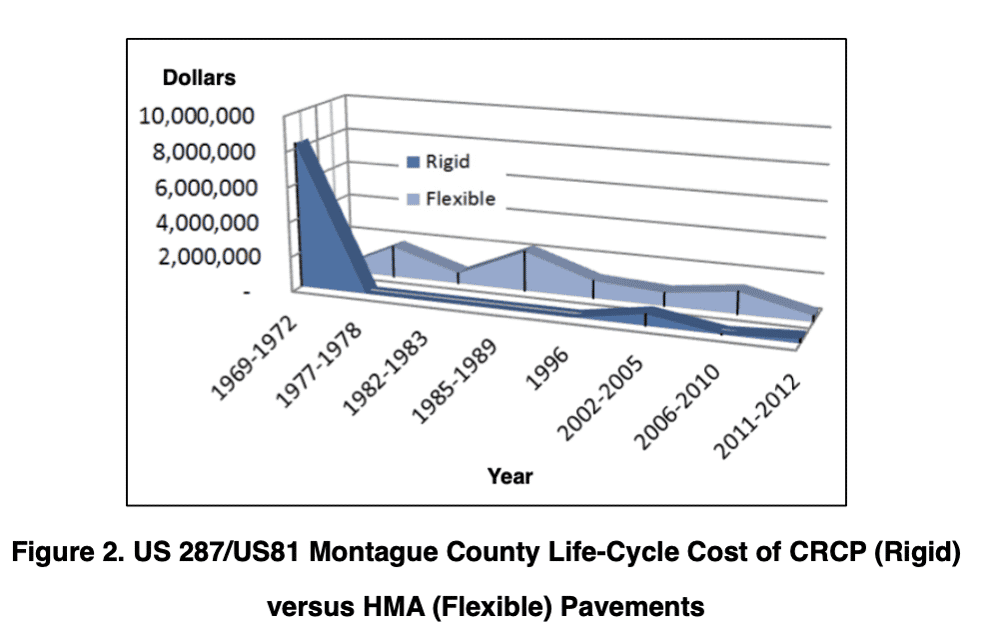
Since then, the initial cost difference between concrete and asphalt has become more competitive, potentially leading to greater savings. Currently, the Cement Council of Texas is seeking to collaborate with the Wichita Falls District to update the life-cycle cost analysis of CRCP versus HMA pavements in Montague County.
Sustainability
Over the last several years, the focus on sustainability has increased dramatically and the concrete and cement industry has set a goal of reaching carbon neutrality throughout the construction value chain by 2050. With respect to concrete pavements, there are two broad based strategies that can be used to improve a concrete pavement’s sustainability and lower its Life Cycle CO2 emissions. The first strategy is to improve pavement and concrete mix designs so that the pavements last longer and have lower embodied CO2 from the initial construction. The second strategy is to reduce the “Use Phase” impacts. Pavements are long-term investments that are intended to last for decades, and the use phase accounts for the CO2 emissions of the public as they drive on the pavements. While much of the current emphasis is on reducing a pavement’s embodied CO2 emissions, use phase emissions can dominate the materials, construction, and maintenance and rehabilitation phases, especially on high volume truck corridors where CRCP are most often used.
With respect to the embodied CO2, most designers and engineers automatically assume that CRCP have a much higher embodied CO2 compared to JPCPs, with dowels, because of the extra amount of streel. However, based on our analysis, the initial CO2 emissions difference between comparable JPCP and CRCP is only between 6.5% and 9% depending on pavement thickness. While one can argue whether this is a large amount or not, the true savings emerge during the use phase, where CRCP outshine all other pavement systems owing to their exceptional long-term performance and the reduced “Pavement Vehicle Interaction” or PVI.
PVI is the increased or excess rolling resistance that occurs between the vehicle and the pavement, which increases the fuel consumption required to move the vehicle and causes additional CO2 emissions. In the USA, PVI is primarily a function of two components of the pavement system: roughness and stiffness. As a vehicle moves over a pavement, any roughness or irregularity in the surface will “bounce” the car or truck, which engages the vehicle’s suspension system and decreases the vehicle’s fuel efficiency. The rougher the pavement is, the greater the loss of fuel efficiency and the greater the CO2 emissions associated with using the pavement. Thus, it is important to build smooth pavements that can maintain their smoothness throughout the life of the pavement. Similarly, when a vehicle drives on a pavement, the pavement deflects, and the vehicle must continuously drive uphill to overcome the deflection. Stiffer pavements, such as concrete pavements, deflect less under the weight of the heavy vehicles and that lowers the excess PVI fuel consumption.
The best-performing pavements exhibit smoothness and stiffness, and CRCP pavements are inherently the stiffest pavement system, tending to remain the smoothest the longest. TxDOT has extensive International Roughness Index (IRI) data on pavements dating back to 1996, categorized by age for CRCP in Figure 3. This data demonstrates that CRCP maintains low and consistent IRI values across various age groups, indicating excellent smoothness and durability over time. Even as CRCP sections age beyond 30 years, the IRI remains relatively low, highlighting its long-term performance and minimal maintenance requirements. Consequently, CRCP has the lowest PVI-related environmental impacts of any road pavement system. These impacts can be further reduced, especially on higher volume roadways, by using techniques such as diamond grinding to enhance concrete pavement smoothness at initial construction or throughout its lifetime.
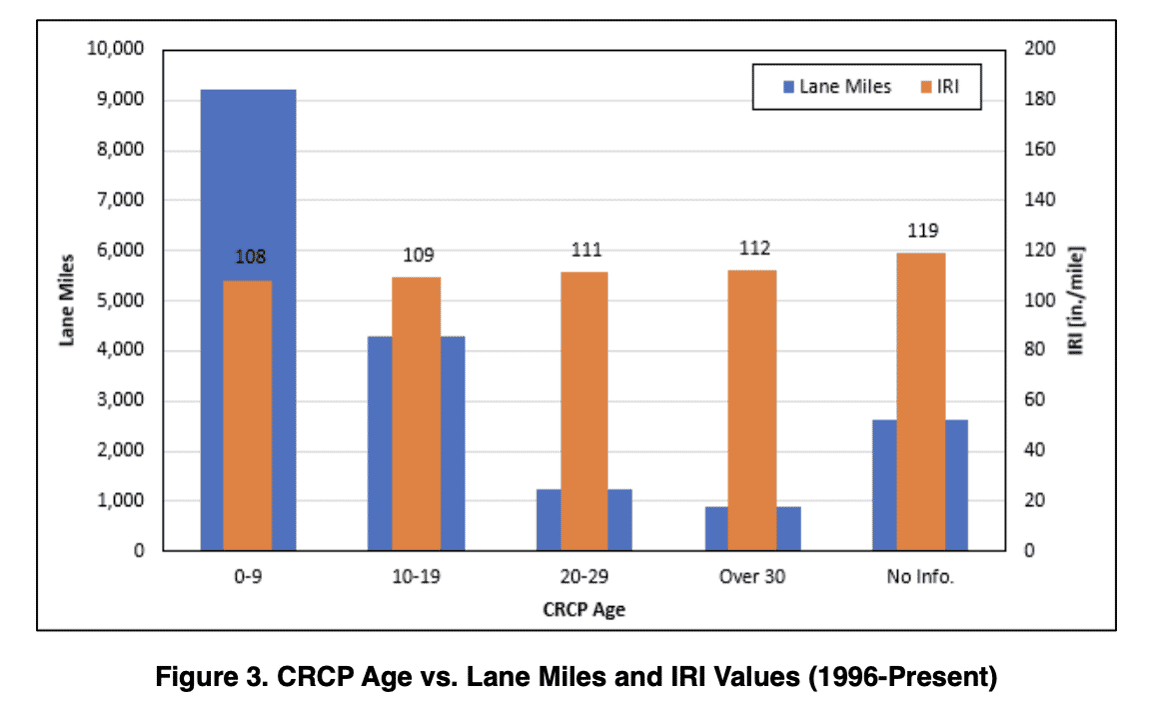
The other big savings come from reduced maintenance and rehabilitation activities. As a general guideline, anytime there is congestion, a vehicle’s fuel efficiency decreases because of increased idling time, stop and go traffic, and increased travel time. Most asphalt pavements require rehabilitation approximately every 10 and 15 years and most JPCP need their first rehabilitation sometime between 25 and 35 years. CRCP are long term pavements and have lasted over 40 years before requiring their first rehabilitation activity, with many lasting much longer than that (e.g., parts of I-610 in Houston are approaching 65 years). With fewer rehabilitation activities and work zones, there is automatically reduced congestion, decreased idling times, minimized stop-and-go traffic, and faster travel times. These factors collectively contribute to lower CO2 emissions.
Challenges and Considerations
Many of the challenges encountered in conventional concrete pavements are also applicable to CRCP. These include climate variability, expansive soils, and construction quality. Given Texas' vast size, the state experiences diverse climatic and soil conditions that can affect the design and construction of CRCP. It is crucial to account for these climate variations and their potential impact on pavement lifespan. Additionally, conducting thorough testing to assess soil types and determine appropriate treatments is essential for ensuring robust structural support for CRCP installations.
In regions where expansive soils are prevalent, it is paramount to implement appropriate treatments to mitigate the potential challenges they pose for CRCP. Expansive soils have the tendency to undergo significant volume changes in response to variations in moisture content, which can lead to soil movement and subsequent pavement distress. One effective approach involves implementing soil stabilization techniques to minimize the detrimental effects of expansive soils on pavement performance. Soil-cement stabilization is often recommended as an effective solution to help mitigate the detrimental effects of moisture-induced volume changes by reducing soil swell potential and increasing its strength and stiffness. Testing is strongly recommended to ensure the selection of the most suitable stabilizer and its appropriate dosage. Additionally, proper subgrade preparation and drainage measures can help manage moisture levels within the soil, thereby mitigating the risk of expansive soil-induced damage to CRCP.
Achieving proper construction quality is crucial for the long-term performance of CRCPs. Challenges such as achieving adequate compaction of the supporting layers, proper placement of reinforcement, and minimizing construction-related defects require attention to detail and effective quality control measures. By implementing rigorous quality control protocols, construction teams can ensure the long-term performance and durability of CRCP, thereby maximizing their lifespan and minimizing maintenance requirements.
Ultimately, addressing the challenges present in CRCP requires collaboration among engineers, designers, contractors, and transportation agencies to develop effective design, construction, maintenance, and rehabilitation practices tailored to Texas' specific conditions and requirements.
Conclusion
In conclusion, continuously reinforced concrete pavements play a vital role in enhancing infrastructure sustainability and minimizing maintenance costs in Texas. Their inherent durability and low maintenance characteristics make them a preferred choice for highway pavements, especially in regions with heavy traffic and diverse weather conditions. By adhering to design principles that emphasize proper reinforcement placement, crack control, and adequate pavement thickness, CRCPs can withstand the rigors of Texas' climate and traffic loads while offering longevity of nearly 40 years with minimal to no repairs. Additionally, CRCPs provide significant cost benefits over their lifecycle due to decreased maintenance needs and prolonged service life. This is supported by TxDOT's analysis, which indicates an average service life of 39.5 years before the first rehabilitation for CRCPs in Texas, suggesting that CRCPs have the potential to last even longer. Moreover; CRCPs contribute to sustainability efforts by minimizing carbon emissions during the use phases and reducing congestion through fewer maintenance activities, ultimately benefiting the environment and road users alike. Despite facing challenges such as climate variability and expansive soils, implementing effective soil stabilization techniques and rigorous quality control measures can ensure the successful performance of CRCP in Texas. Through collaboration and innovation, CRCP technology will continue to evolve, offering sustainable and cost-effective solutions for the state's transportation infrastructure needs.
Acknowledgments
The authors would like to express their sincere gratitude to the Texas Department of Transportation (TxDOT) Maintenance Division for their invaluable assistance. We deeply appreciate their thorough review and revision of our work, as well as their generous provision of the necessary data.