Mass Concrete: The Importance of Aggregate Gradation
Mass concrete is primarily used in large-scale construction projects where the dimensions of the concrete structure require careful management of heat generated during the curing process. Common applications include dams, bridge piers, large foundations, and retaining walls, where the substantial volume of concrete necessitates special considerations to control temperature and prevent thermal cracking.
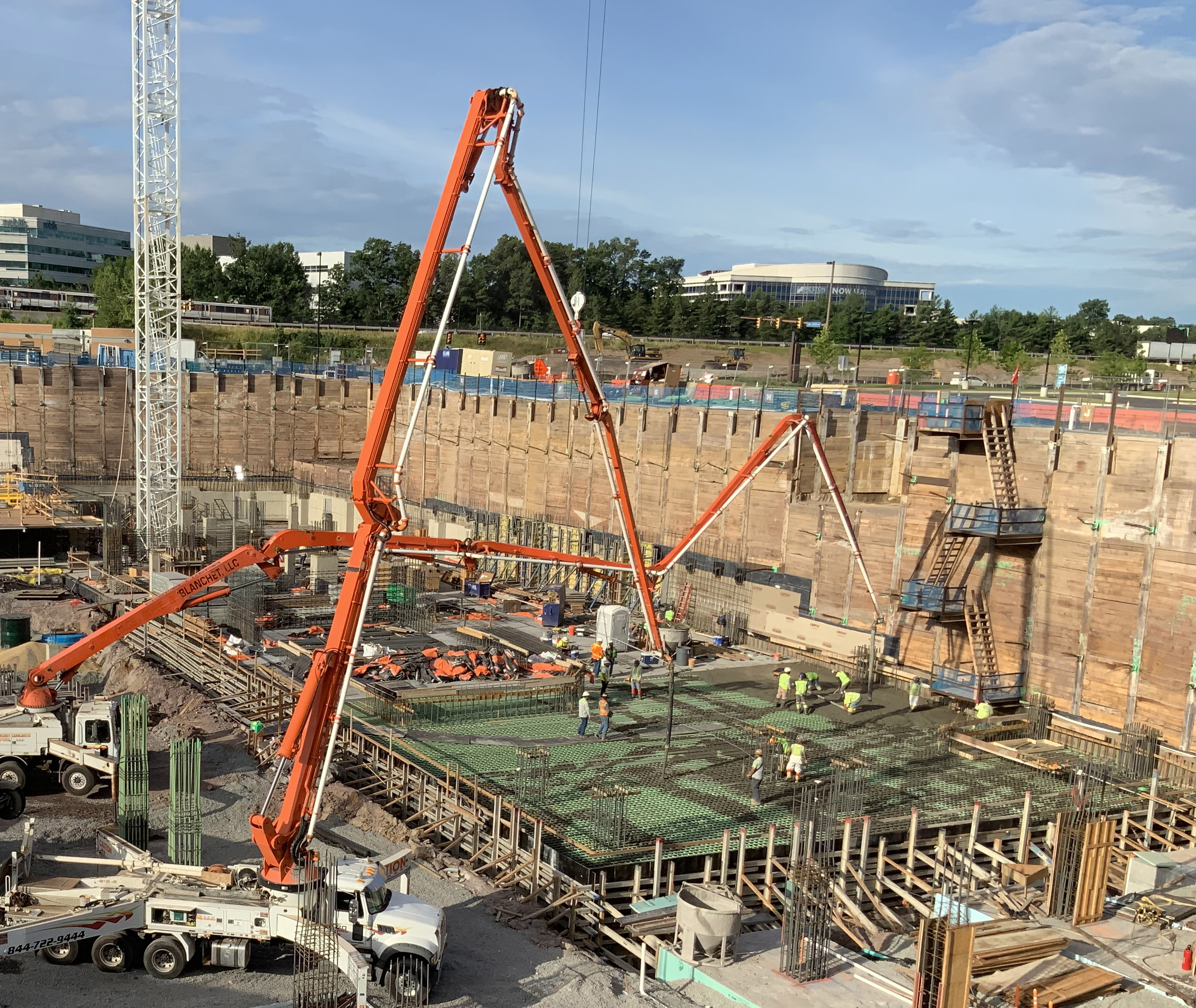
In infrastructure projects like highway overpasses and industrial facilities, mass concrete provides the necessary strength and durability to withstand heavy loads and environmental stresses. Additionally, its use in gravity structures, such as spillways and large footings, highlights its capacity to resist significant structural forces. The unique challenges of mass concrete demand careful attention to mix design, material selection, and thermal control strategies to ensure long-term stability and performance.
Figure 1 illustrates a project involving the construction of a 5,000 cubic yard mass concrete mat foundation for the Children’s Hospital in Houston, TX, completed by Carrasquillo Associates. This large-scale foundation required careful planning and execution to manage the heat of hydration and ensure long-term structural integrity.
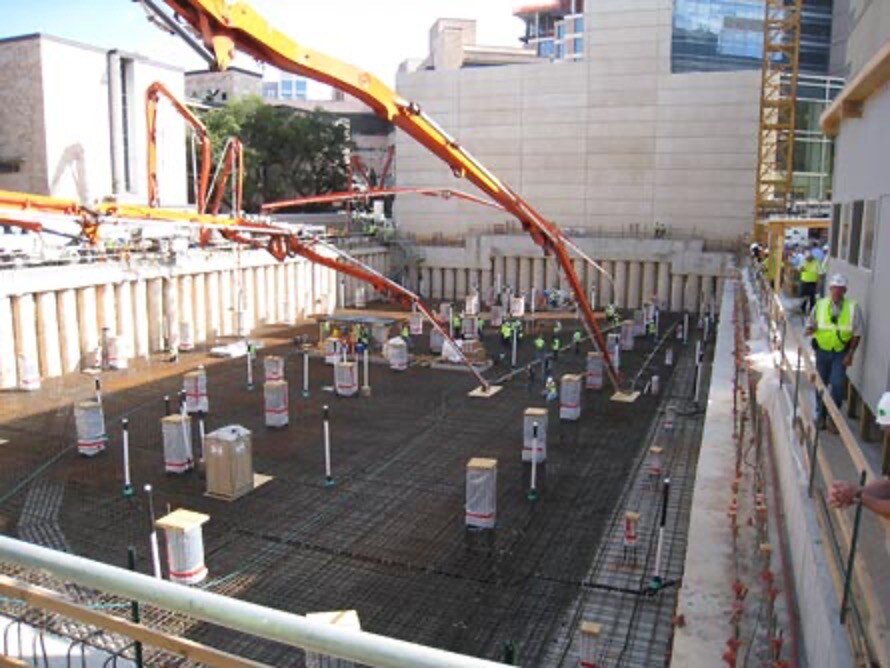
Figure 1. Mass Concrete Mat Foundation for the Children’s Hospital in Houston, TX. Extracted from: http://m.carrasquilloassociates.com/project/texas-childrens-hospital-mass-concrete-placement/
Heat of Hydration in Mass Concrete
Heat hydration in mass concrete occurs when the cement reacts with water, generating significant amounts of heat due to the exothermic nature of the reaction. In large structures, this heat can become trapped, leading to temperature differentials between the interior and exterior of the concrete, which can cause thermal stress and cracking. To mitigate this risk, mass concrete mix designs often utilize larger aggregate sizes and reduce the cement content compared to conventional concrete. These strategies, along with techniques such as cooling or insulating the concrete, help minimize heat generation during curing, reduce the risk of thermal cracking, and enhance the long-term durability of large structures.
Workability and Placement in Mass Concrete
Workability is crucial in mass concrete because large volumes of concrete need to be placed uniformly and efficiently. Poor workability can cause issues such as aggregate segregation, difficulty in placing the concrete, and problems with compaction. These challenges are amplified in mass concrete projects due to their size. By optimizing aggregate gradation, the mix's workability can be greatly improved. A well-graded aggregate structure promotes better flow of the concrete mix, reducing the need for excessive water or chemical additives that would otherwise increase paste volume. This leads to more consistent and uniform compaction, which is vital for avoiding cold joints or weak areas within the structure.
Durability and Long-Term Performance of Mass Concrete
The durability of mass concrete is not just dependent on strength but also on its ability to withstand environmental factors such as moisture infiltration, temperature changes, and freeze-thaw cycles. Proper aggregate gradation is a key factor in creating a durable mass concrete mix as it helps reduce the permeability of the concrete, which directly influences the material’s resistance to water infiltration and freeze-thaw damage. By creating a dense, low-void structure, the concrete is better able to prevent water penetration, significantly extending its long-term performance and reducing the risk of long-term damage.
The Hoover Dam is an excellent example of a mass concrete structure that demonstrates long-term performance. Completed in 1936, this massive structure has withstood the test of time for nearly 90 years. The Hoover Dam is composed of approximately 3.25 million cubic yards of concrete, making it one of the largest mass concrete projects in history.
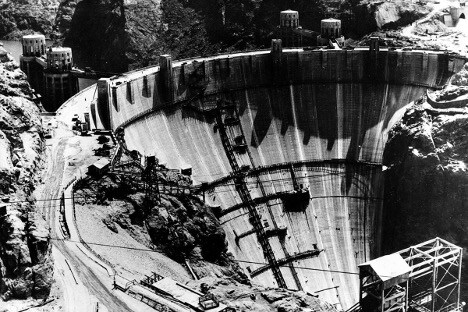
Figure 2. The Hoover Dam in Construction in 1935
Optimizing Aggregate Gradation in Mass Concrete with the Tarantula Curve
The Tarantula Curve is a powerful tool for optimizing the aggregate gradation in concrete mixes, and its application to mass concrete offers distinct advantages in managing the challenges posed by large-volume placements. As explained above, one of the key strategies to reduce the risk of thermal cracking is minimizing the cement content, as cement is a major source of heat generation in the curing process. However, reducing the paste content in mass concrete must be done carefully to avoid compromising workability and durability. This is where the Tarantula Curve comes into play by providing a guideline for optimizing aggregate gradation to achieve a dense and well-graded mix that requires less paste while maintaining the necessary flow and placement characteristics.
Figure 3 illustrates the Tarantula Curve, which represents the recommended proportions of aggregate sizes retained on various sieves for an optimal concrete mix. The x-axis shows the sieve numbers, starting from finer sizes (l#200) to coarser sizes (1.5 inches). The y-axis indicates the percentage of material retained on each sieve size.
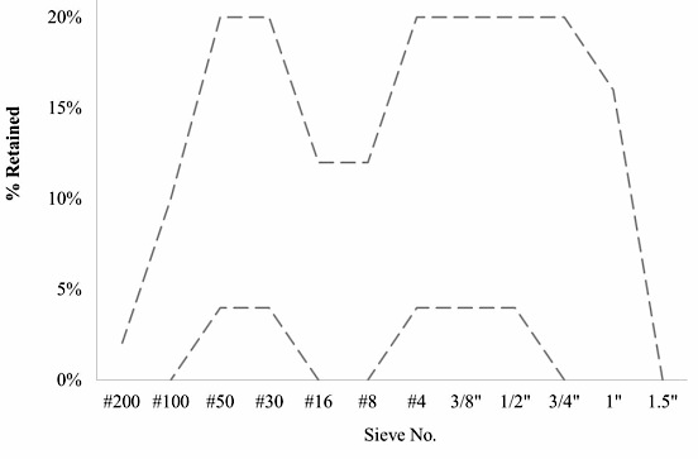
Figure 3. The Tarantula Curve
To apply the Tarantula Curve in mass concrete, the process begins with selecting a range of fine, intermediate, and coarse aggregates that complement one another. The goal is to create a balanced aggregate gradation, where each size of aggregate fills the voids created by the next larger size, resulting in a densely packed mix. The Tarantula Curve provides specific guidance on the ideal proportions of each aggregate size, helping to ensure that the mix stays within the optimal range for achieving a dense, efficient packing structure.
Once the appropriate aggregates are selected, engineers plot the gradation of the mix on the Tarantula Curve graph, which consists of recommended upper and lower bounds for each aggregate size. This allows for adjustments to be made to ensure the mix falls within these limits, ensuring minimal void content and optimal packing density. Conducting sieve analyses and adjusting aggregate proportions based on the curve leads to a concrete mix that has superior workability, reduced paste content, and improved long-term durability.
For more information about the Tarantula Curve visit http://www.tarantulacurve.com/
Conclusion
In conclusion, mass concrete structures present unique challenges due to their size and the heat generated during the curing process. Proper management of the heat of hydration, workability, and long-term durability are essential for ensuring the success of these large-scale projects. By using larger aggregate sizes, reducing cement content, and optimizing mix design, engineers can effectively mitigate the risks associated with thermal cracking and enhance the concrete's long-term performance.
The Tarantula Curve provides a crucial framework for optimizing aggregate gradation in mass concrete applications. By carefully selecting and balancing fine, intermediate, and coarse aggregates, engineers can reduce paste content while maintaining excellent workability and durability. This approach not only improves the performance of the concrete but also contributes to more sustainable, cost-effective construction practices.