Circular Construction Using Recycling Materials
In an increasing effort to provide more sustainable construction practices, our industry is moving toward circular construction. One of the most impactful changes we can make is using recycled construction materials in our projects. Not only does this practice help conserve natural resources and reduce landfill waste, but it also offers economic benefits by lowering material costs and decreasing the carbon footprint of construction activities. By embracing recycled construction materials, we can build a more sustainable future while maintaining the strength and durability our projects demand.
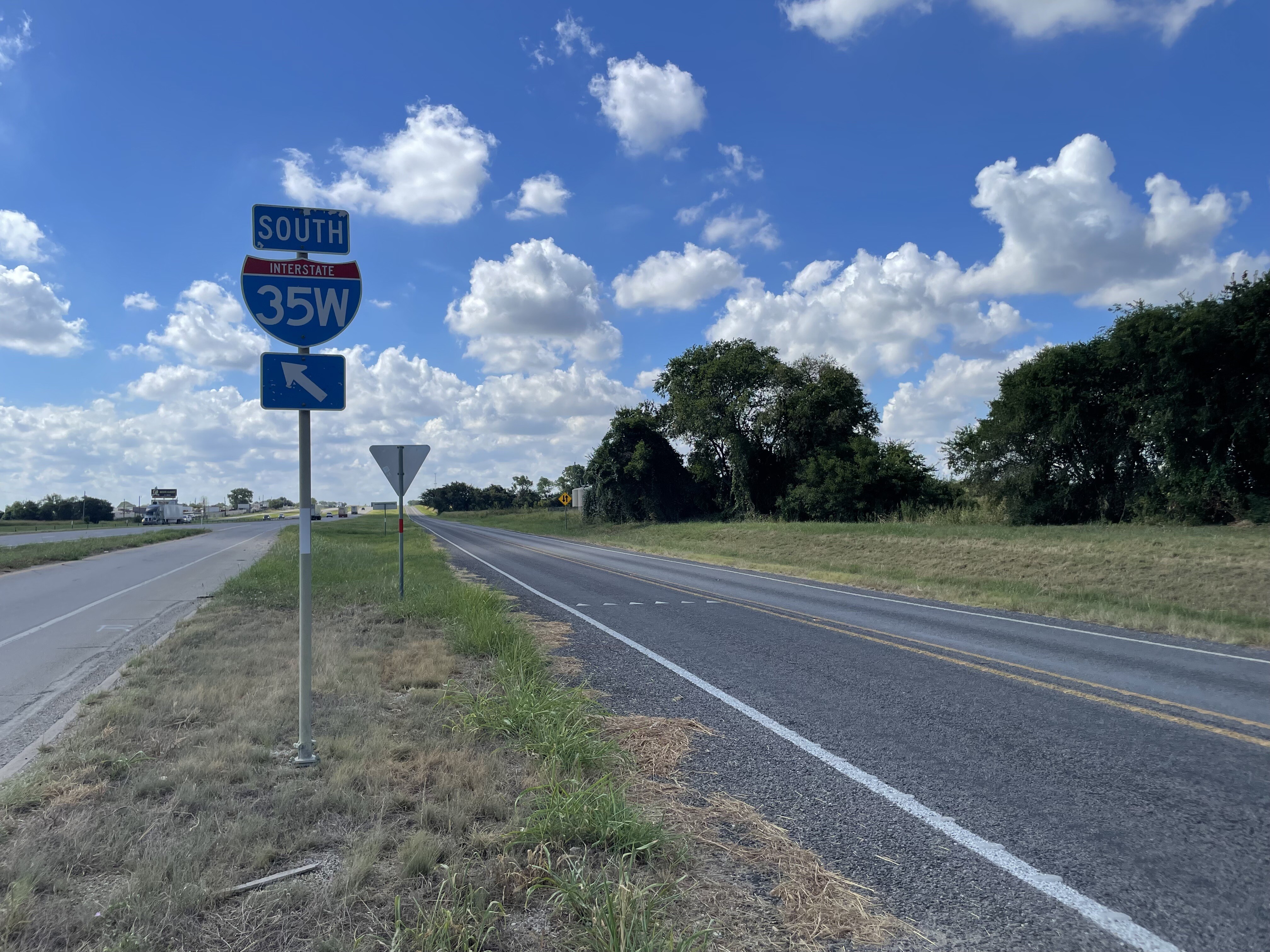
Surface Pavement
When a concrete pavement completes its service life of 40 to 60 years, or if a roadway segment is abandoned due to a change in the roadway geometry, the original materials used to build that concrete still have value. The crushed concrete aggregate can be graded and reused in numerous new concrete applications. In a world of environmental concern and limited resources, crushing and recycling concrete pavement is a genuine cost-saving measure. Avoiding sending significant segments of old concrete pavement to our landfills is simply the right thing to do. Additionally, crushed concrete pavement can find new life as a cement-treated road base that can be used as an underlayment for a new concrete pavement or used as a base for a new flexible pavement road.
Field performance evaluations of concrete pavements have revealed that a durable, stabilized, non-erodible base is essential to the long-term performance of concrete pavements. If the base does not provide good support, the concrete pavement will be compromised, and long-term performance might be compromised. Texas Department of Transportation studies have proven that a cement-stabilized base is the most durable, resilient, and economical solution. There are numerous examples of successful projects that saved taxpayers’ dollars by reusing the old pavement in this way and the practice is becoming more routine.
Road Base
Cement stabilization is an excellent and widely accepted method for building durable and resilient pavement. Recycling road-based materials with cement is a commonplace practice. The materials that can be used are:
- Gravel
- Shell
- Crushed stone
- Slag
- Recycled Hot Mix Asphalt (HMA)
- Recycled concrete
- Incidental Sand, Silt, and Clay
Full Depth Reclamation (FDR) with cement is a form of recycling that is used all across Texas, the United States, and the World. The consensus is that this method of recycling should save 30 to 50 percent of the cost of a removal and replacement strategy. The reasons for this savings include:
- Time savings: FDR has fewer construction challenges than traditional pavement rehabilitation. There is no removal of the existing pavement. There is no replacement of the existing base and no hauling of materials unless the elevation is changed. And there is no re-preparing the subgrade. Everyone knows time is money.
- Reduced Project Impacts: There is less disruption to the property owners and for roadway users. There is less equipment and fewer haul trucks.
- Reduced project waste and fuel consumption: Unnecessary roadway material waste is eliminated and because less equipment is needed, fuel consumption is reduced.
Building cement-treated base with quality crushed aggregate is generally preferred, but it is not always necessary. Depending on the type of roadway being built, even poor material can become a good road base by incorporating cement stabilization. In the Rio Grande Valley of South Texas, housing subdivision streets were built using untreated local caliche as a road base. This weak untreated crushed limestone material was overlaid with asphalt and the pavement soon failed. When full-depth reclamation with cement was performed, these roads became durable and received long-lasting life.
TxDOT applied a mandate to stockpile Recycled Hot Mix Asphalt. Of course, the highest and best use of these materials is to incorporate them into new asphalt pavement, but many times these stockpiled materials were either unsuitable for reuse in the surface pavement or unusable altogether due to oxidation, defects, hauling, or handling costs.
In response to the need to remove the massive and unsightly stockpiles of unused or unsuitable HMA material, the Johnson County Area Office of TxDOT was authorized to donate these materials as part of the County Assistance Program in amounts beyond what was required, and stockpiles remained substantial. It was determined that these materials should be added to the FDR program that was put together in response to widespread damage to untreated base roadways due to the Barnet Shale Oil Boom equipment traffic. Many roadways were rebuilt using FDR with cement and surplus HMA material. In one case, unsightly stockpiled HMA material contaminated with milled Petromat fabric remained on the State right-of-way for years due to the belief that it was unsuitable for any use. This substantial amount of material was successfully used with the material on the existing severely damaged pavement and mixed with cement on the IH 35W frontage roads between Alvarado and Grandview. The mammoth stockpiles were eliminated, resulting in resilient and durable roadways.
Subgrade
Every good road builder knows that you build good pavement starting at the bottom and working up. Subgrade improvement can go a long way toward building longer-lasting roads. In areas with high Potential Vertical Rise (PVR), stronger and thicker subgrade improvements can buttress the pavement against the pressure caused by the natural swelling of the soil at a significantly lower cost than using thicker pavement. Traditionally in Texas, the standard subgrade improvement thickness is 8 inches for highways and 6 inches for city streets. In the areas of higher PVR, 12-24 inches of subgrade improvement is common, and 36 inches is generally considered the usual depth of influence. Treating the high-swell soils with a combination of lime and cement will ensure that this subgrade layer will not swell again. This new chemically treated subgrade will be a permanent layer where the clay particles in the soil are flocculated by the lime, there is immediate strength added by hydration using cement, and more delayed strength is added with the pozzolanic properties of lime and cement together. Laboratory testing is recommended for these areas of deep subgrade improvement. First, add sufficient lime to reduce the plasticity index to 20 and ensure flocculation of the soil particles, and then do a cement series to ensure that a target 7-day Unconfined Compressive Strength (UCS) test meets the project requirements. Many times, without combination with cement, clay soil may fail to have an adequate UCS that will both support the pavement and resist subgrade pressure due to the swelling of the soil. During construction, if a subgrade using lime alone fails to stabilize, the solution is to keep adding more lime—this lack of certainty results in substantially over-running the budget for lime stabilization. The combination of lime and cement percentages determined in the laboratory will ensure that the quantities in the field will not overrun the project’s budgeted amounts.
When using the combination of lime and cement in cases where sulfate amounts are significant, a mellowing period of 3-7 days is recommended for each lift after adding lime. After cement treatment, additional lifts of pavement can proceed immediately. Alternatively, a remove-and-replace strategy could be considered, but the cost of doing this would be significantly higher than that of preserving the existing subgrade and without the high costs of hauling off existing materials and hauling in new materials.