The Birth of RCC at Fort Cavazos
RCC was developed in the 1960s and 1970s to address the need for economical and durable pavement solutions. Combining the construction techniques of asphalt with the strength and durability of Portland cement concrete, RCC quickly gained recognition for its cost-effectiveness and robustness. In 1983, Fort Cavazos became one of the earliest adopters of RCC, laying down the pavement that would stand the test of time.
The 1983 RCC pavement project consisted of a 500 by 328-foot tank parking area, covering an area of approximately 18,222 square yards. Initially, the design called for a thicker pavement, but due to machinery constraints, a 10-inch pavement was ultimately selected, which turned out to be highly effective. The foundation of the pavement includes a 6-inch layer of base material over a 6-inch layer of lime-treated subgrade.
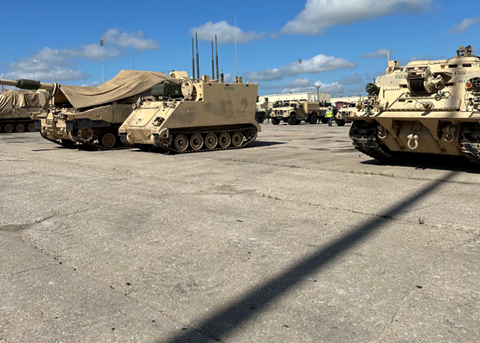
Figure 1. 40-Year-Old 10-inch RCC Pavement at Fort Cavazos Supporting Military Tanks
The initial construction of RCC at Fort Cavazos involved some trial and error. At the time, there was limited knowledge about joint control in RCC pavements. Natural joints and cracks were utilized instead of saw cuts, a practice that has since evolved with better understanding and techniques. Despite these early challenges, the RCC pavement demonstrated exceptional load-bearing capacity and durability.
Proven Performance
Four decades later, the RCC pavement at Fort Cavazos continues to support the heaviest military equipment, including tanks and other heavy vehicles. The original surface, as shown in Figure 2, was diamond ground for a smooth finish and remains intact today. This enduring durability is a testament to the material’s resilience and the foresight of the engineers who implemented it.
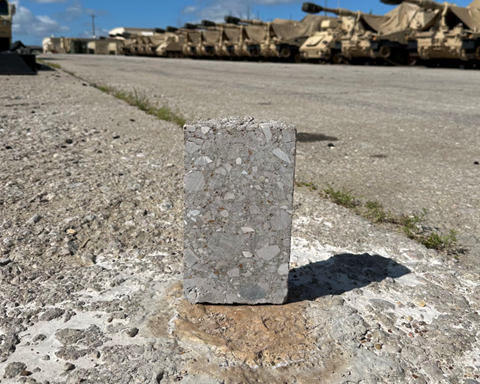
Figure 2. Core of the 40-Year-Old RCC Pavement (recorded strength of 9,000 psi)
Since its construction in 1983, the RCC pavement at Fort Cavazos has required no maintenance whatsoever. This impressive longevity is a testament to the exceptional durability and resilience of Roller-Compacted Concrete. Despite the heavy loads and frequent use associated with a military base, the pavement has maintained its structural integrity and functionality without the need for repairs or upkeep. This lack of maintenance not only underscores the reliability of RCC but also translates to substantial cost savings and reduced operational disruptions, further proving its value as an ideal material for long-lasting infrastructure.
Evolution of Construction Techniques
Over the years, RCC construction techniques have advanced significantly. In the 1980s, motor trowels and regular paving machines were used, resulting in rough finishes. Today, high-density laydown machines and improved finishing methods ensure smoother surfaces and more efficient construction processes. These advancements have further cemented RCC's reputation as a reliable and practical pavement solution.
Economic and Environmental Benefits
One of the key reasons for the rapid acceptance of RCC worldwide is its economic advantage. In the 1980s, the cost of RCC was approximately $43.53 per cubic yard, a fraction of today’s conventional concrete costs, which can be around $200 per cubic yard. Additionally, RCC’s ability to use a broader range of materials and its zero-slump consistency allow for immediate placement of subsequent lifts, enhancing construction efficiency and reducing environmental impact.
Looking Forward
The ongoing construction at Fort Cavazos showcases the efficiency and effectiveness of using RCC over traditional pavement methods. Covering approximately 26,000 square yards, this project involves replacing an existing asphalt pavement with a 9-inch RCC pavement over a robust foundation comprising a 6-inch cement-treated base (CTB) atop a 6-inch lime-treated subgrade. The RCC slab is designed with 16 by 16-foot joint spacing and is finished using a motor trowel, ensuring a smooth surface. Figure 3 illustrates the 9-inch RCC pavement and its ability to support heavy military vehicles, showcasing its strength and durability.
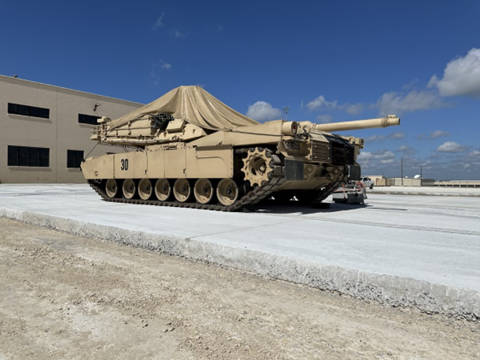
Figure 3. 9-inch RCC Pavement Supporting a Military Tank
Remarkably, the entire RCC pavement project is slated for completion within just 7 days—a significant reduction in time compared to traditional paving methods, which could take over four months using a night schedule. Furthermore, RCC's rapid-set properties allow it to be opened to traffic within just one day of placement and can support heavy loads of up to 72 tons within 20 hours. This swift turnaround not only minimizes disruption but also underscores RCC's superior durability and cost-effectiveness, making it an ideal choice for projects requiring quick completion without compromising on quality.